Bioprocess 4.0 promises a digitised and automated future for the biopharmaceutical industry in the form of a Process Analytical Technology (PAT) solution, offering many benefits including increased quality and quantity of product, as well as a way of handling and processing the data-load generated by a technologically augmented process.
In this article I will go over four reasons why you need a PAT solution to modernise as well as future-proof your development and manufacturing infrastructure.
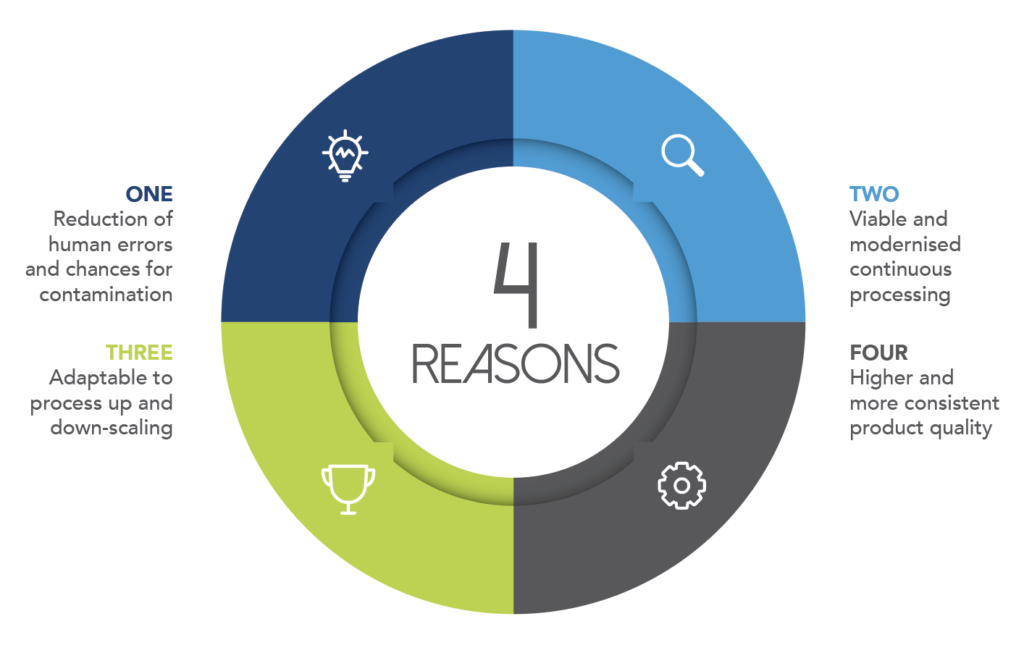
1.Reduction of human errors and chances for contamination
A fully implemented PAT solution such as the one offered by Securecell enables a process as well as its associated analytics to be pre-planned and automated. TheLucullusPIMS planning and operation tools provide the functionality to design and execute an entire bioprocess with only one click, while the online tool allows for simultaneous monitoring, control and automation of all the process equipment in use. This minimises the need for human intervention and the chances of errors as well as contaminations to occur. Furthermore, using theNumeraautosampler and analyser, process sampling can also be pre-planned, and samples taken, prepared, analysed, and stored throughout the process cycle fully autonomously while maintaining sterility throughout.
2. Viable and modernised continuous processing
Industry trends in biopharma have been shifting away from batch towards continuous manufacturing for a number of years. This has been partly attributed to increased demand for operational streamlining, lower production costs, consistency of product, and other economic benefits. However, one of the challenges with continuous processing is finding a way to handle the sheer amount of data it produces. PAT solutions offer a way not only to collect this process data, but to digitise and centralise it while monitoring and controlling your process in real time. TheLucullusGraphic tool can be used to load not only historic processes, but ongoing ones as well, which can be directly compared to past runs in order to evaluate any changes in circumstances or conditions. Efficient and effective data handling of passed and ongoing manufacturing processes facilitates viable and digitised continuous processing.
3. Adaptable to process up and down-scaling
A PAT solution can be integrated from the very beginning of the bioprocess development phase. The data generated assists in the scalability of the process, and the technology can follow the process all the way to large scale manufacturing. For example,LucullusandNumera可以适当地实现小范围吗benchtop laboratory and with full CFR21 Part11 compliance, a large scale GMP manufacturing facility. Using the Lucullus graphic tool, data from the very beginning of the development phase can be directly compared with and assist in the scale up of a given process at any point within its development phase.
4. Higher and more consistent product quality
PAT solutions are able to interface with the various sensors associated with live process equipment (such as bioreactors), allowing them to measure process critical parameters (CPPs) in real time. Furthermore, the software is powerful enough to process this live data stream and apply smart feedback algorithms that feed back to the equipment to ensure that CPPs and by extension, their respective critical quality attributes remain within strictly defined parameters. TheLucullusPIMS operation and online tools provide the functionality to do this with up to 8 bioreactors simultaneously, improving not only yields but also ensuring a higher and more consistent quality of product.
If you are interested in hearing more about the exciting PAT solution offered bySecurecell, please contactSean Doran在英国石油公司。